AI's Impact on Fleet Parts Management
Artificial intelligence is transforming U.S. fleet management, shifting from reactive to proactive strategies by rapidly analyzing data to predict trends, reduce costs, and minimize vehicle downtime effectively.
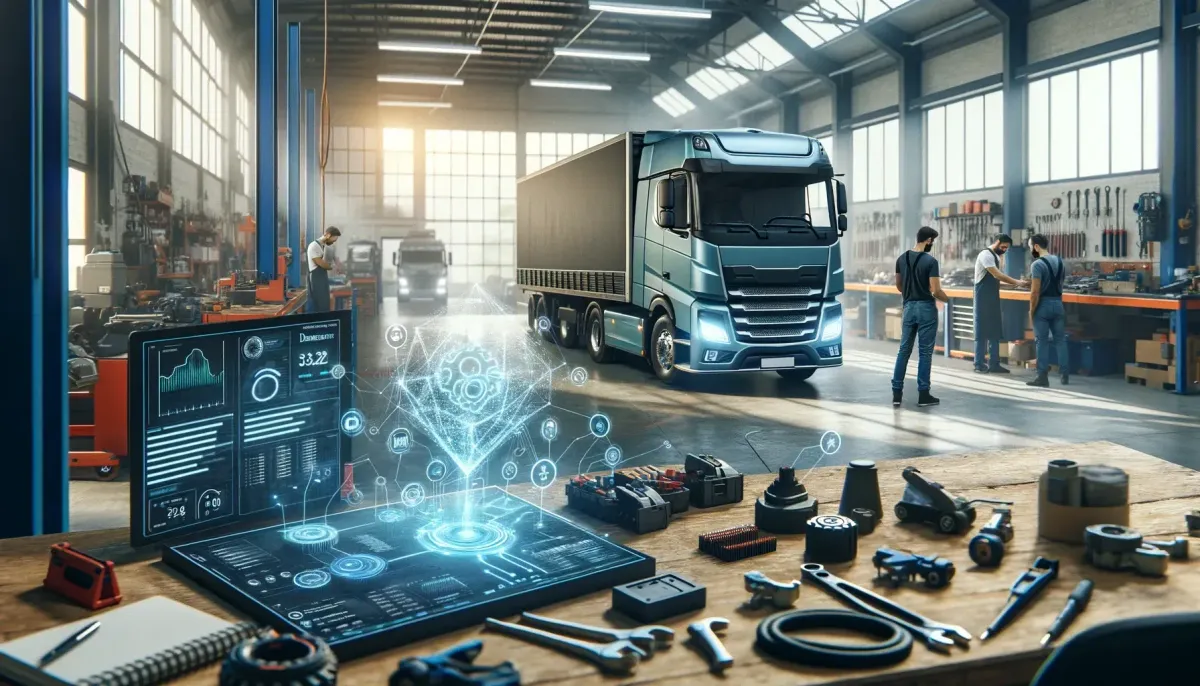
By Neil Pope, for The Inside Lane
Artificial intelligence advancements are transforming fleet management by making the goal of maintaining road-ready vehicles and preemptive maintenance increasingly achievable.
From streamlined parts ordering to inventory optimization, AI technologies can aid fleets in managing their parts inventory to minimize financial losses and significantly reduce vehicle downtime.
"I've talked to shops that don't even know they have a certain part on hand so they end up ordering new ones because they didn't know that they had that sitting on a shelf," Craig Vanderheide, Director of Product Management at Intangles told The Inside Lane.
"There's a lot of unnecessary costs there," the industry leader in predictive maintenance solutions added.
AI’s capacity to analyze vast datasets instantly, identify trends, and make precise forecasts has piqued the interest of industry leaders who are constantly monitoring their bottom line.
Simplifying parts inventory management
Parts inventory management is a multifaceted challenge that significantly impacts operational efficiency.
Maintaining optimal inventory levels is a delicate balance as excess stock carries a financial consideration and leads to wasteful spending, while insufficient inventory can leave trucks stranded and operations in disarray.
How do fleets carry less inventory but not lose on the service that they can provide in terms of quick repairs?
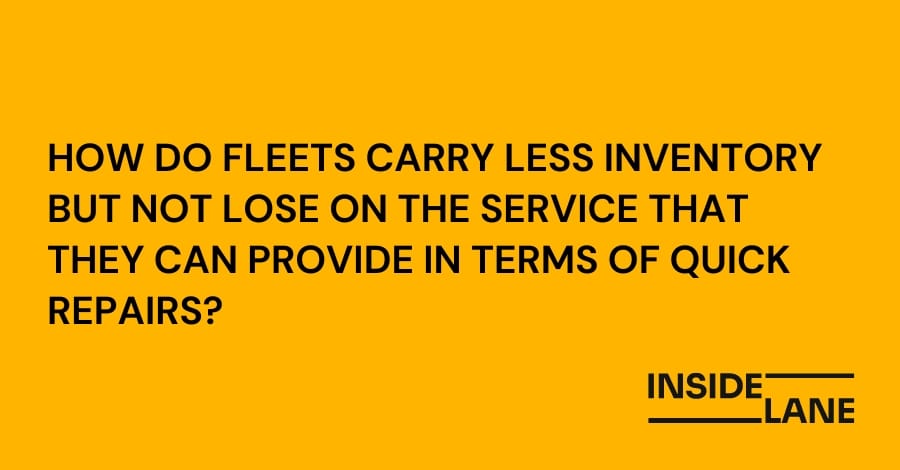
In the realm of AI-driven parts inventory management, the prevailing focus lies squarely on what is being called ‘predictive maintenance’, marking a departure away from the reactive or preventive maintenance schedules prevalent among most U.S. fleets.
The issue with reactive maintenance lies in its reliance on the truck's sensors logging a diagnostic trouble code (DTC) only after a part has failed, in many cases causing a vehicle to break down.
Predictive maintenance collects all the data from a vehicle's sensors and uses AI algorithms to identify patterns that deviate from the normal operating range, even before a DTC has been logged.
This identifies when a part may be showing early signs of failure, allowing early analysis and replacement, before it triggers a vehicle breakdown or causes wear on additional components downstream.
With improved data, insights, and AI tools, managers can now replace parts more precisely, as needed. AI enables fleets to analyze vast amounts of data that would be challenging for a human to process. This allows for better decision-making and enables more strategic inventory purchasing.
AI boosts fleet readiness
The unpredictable nature of breakdowns adds another layer of complexity to inventory management, requiring fleets to be prepared for sudden part failures. This uncertainty can lead to challenges in maintaining the right inventory levels, as fleets respond to breakdowns as they occur.
Jim Rice, President of Uptake, an AI-driven industrial optimization firm, said AI can help fleets be proactive in having the right parts on hand when needed.
"Most fleets are familiar with core parts like air and oil filters. It's the less common ones that can ground a truck," Rice, a 20-year industry veteran told The Inside Lane. "For example, if a sensor breaks, a fleet may not keep it on hand because it’s an expensive part. They’re not as readily available and it's difficult to predict when they'll be needed."

Rice also highlighted the importance of strategic parts purchasing, saying “If you know there are issues with the truck and you can get ahead of it, you're not pigeonholed into buying the part from the guy that can get it there fastest, which can often cost a fleet more money.”
The untapped potential of parts data
Utilizing internal data to drive decisions can reduce wait time for parts, yet many companies are not fully leveraging this valuable resource. Historical data is often used for analyzing past spending and performance, but it's not always utilized to its full potential for future planning.
Fleet managers often find themselves inundated with data, Vanderhede and Rice would argue that the data surrounding parts ordering and inventory is significantly underutilized.
"Modern fleets have superior data, insights, and tools to consume these massive amounts of data that would be challenging for humans to analyze," Vanderheide said. "So you're able to consume more data to make better decisions and more tactical purchasing strategies."
It seems obvious that the industry is encouraging fleets to move beyond simple historical analysis and instead focus on using data to make proactive decisions.
This includes not only understanding what has been spent but also using that information to inform future decisions. However, few companies have adopted this strategy.
"I see numerous shortcomings in the procurement and inventory processes, particularly regarding stocking the appropriate quantity of parts and determining whether to stock aftermarket or OEM parts," Rice said. "There's still a notable level of unnecessary confusion surrounding these areas."
Have a question or comment about this article? Email Bianca Prieto at editor@theinsidelane.co
Not yet subscribed to The Inside Lane newsletter? Join here.
Comments ()