Scaling Smart: People, process and partnerships matter
Gary Kooner dives into the challenges and opportunities of rapid fleet growth.
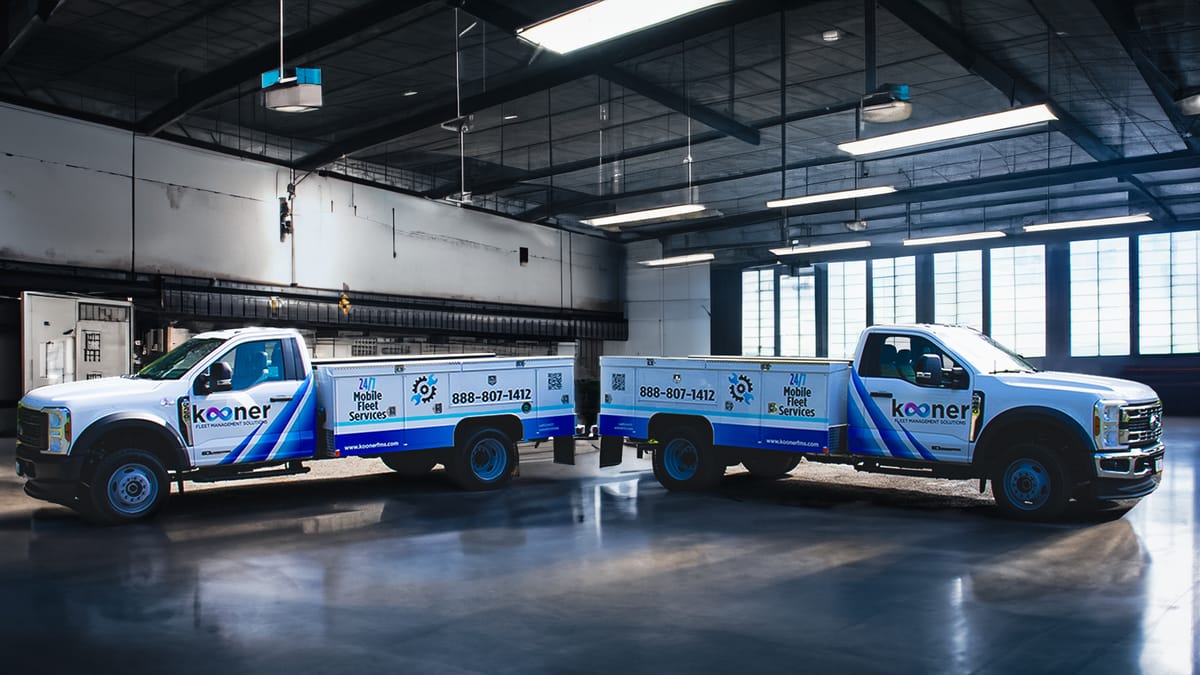
A version of this story first appeared in The Inside Lane newsletter. To get it in your inbox twice a week, sign up for free, here.
By Bianca Prieto | The Inside Lane
Gary Kooner knows what it takes to scale. As the owner of Kooner Fleet Management Solutions, a nationwide mobile and embedded truck repair service company that grew from a single truck to a 250-vehicle nationwide operation in under a decade, he’s faced the challenges that come with rapid growth head-on. In this Q&A, Kooner shares lessons on scaling smart, reducing downtime and using technology to stay ahead in a demanding industry.
What were the biggest challenges in scaling, and what lessons can fleet operators take from your experience?
Scaling so quickly came with significant challenges, but key lessons emerged. Building strong relationships – first locally, then nationally – was crucial for securing reliable partnerships and expanding our network. Identifying and hiring the right talent was equally important; the right people helped drive growth and maintain our high standards. We also focused on developing internal best practices early on, creating systems and processes that supported efficient, sustainable growth. Fleet operators should prioritize people, process, and partnerships. With a strong foundation, it’s possible to grow quickly without sacrificing quality or operational control.
Fleet downtime is a major cost driver. What are the most overlooked maintenance issues that lead to unnecessary downtime, and how can companies address them proactively?
Preventative maintenance is THE most overlooked maintenance issue that leads to unnecessary fleet downtime. Routine oil changes, fuel filter replacements, and air filter maintenance are essential, as failing to address them can cause costly engine damage and reduced fuel efficiency. Companies should track fleet mileage accurately and adhere to manufacturer-recommended maintenance intervals to prevent unexpected breakdowns. Driver education also plays a crucial role. Many drivers lack necessary knowledge about basic vehicle features and pre-trip inspections, leading to preventable issues. Providing thorough training on equipment operation and routine checks ensures early detection of problems, thus reducing downtime and repair costs.
Technology is reshaping fleet maintenance. What innovations are you most excited about, and how should trucking companies adapt to stay ahead?
Technology is revolutionizing fleet maintenance, and the most exciting innovation is the use of real-time data. By equipping fleets with telematics and performance monitoring tools, companies can track fuel usage, vehicle health, and driver behavior instantly. This data enables proactive maintenance, reduces unexpected breakdowns, and boosts overall efficiency. To stay ahead, trucking companies must embrace these tools and invest in training their teams to interpret and act on the insights provided. Making informed, data-driven decisions not only cuts costs but also improves safety and compliance. The future of maintenance is predictive – and it starts with knowing your fleet inside and out.
This interview was edited for brevity.
Thanks for reading The Inside Lane! You can reach the newsletter team at editor@theinsidelane.co. We enjoy hearing from you.
Would you like to be featured in an upcoming edition? Shoot us an email.
Interested in advertising? Email us at newslettersales@mvfglobal.com
The Inside Lane is curated and written by Shefali Kapadia and edited by Bianca Prieto.
Comments ()